Shop by Category
All CategoriesInspiration
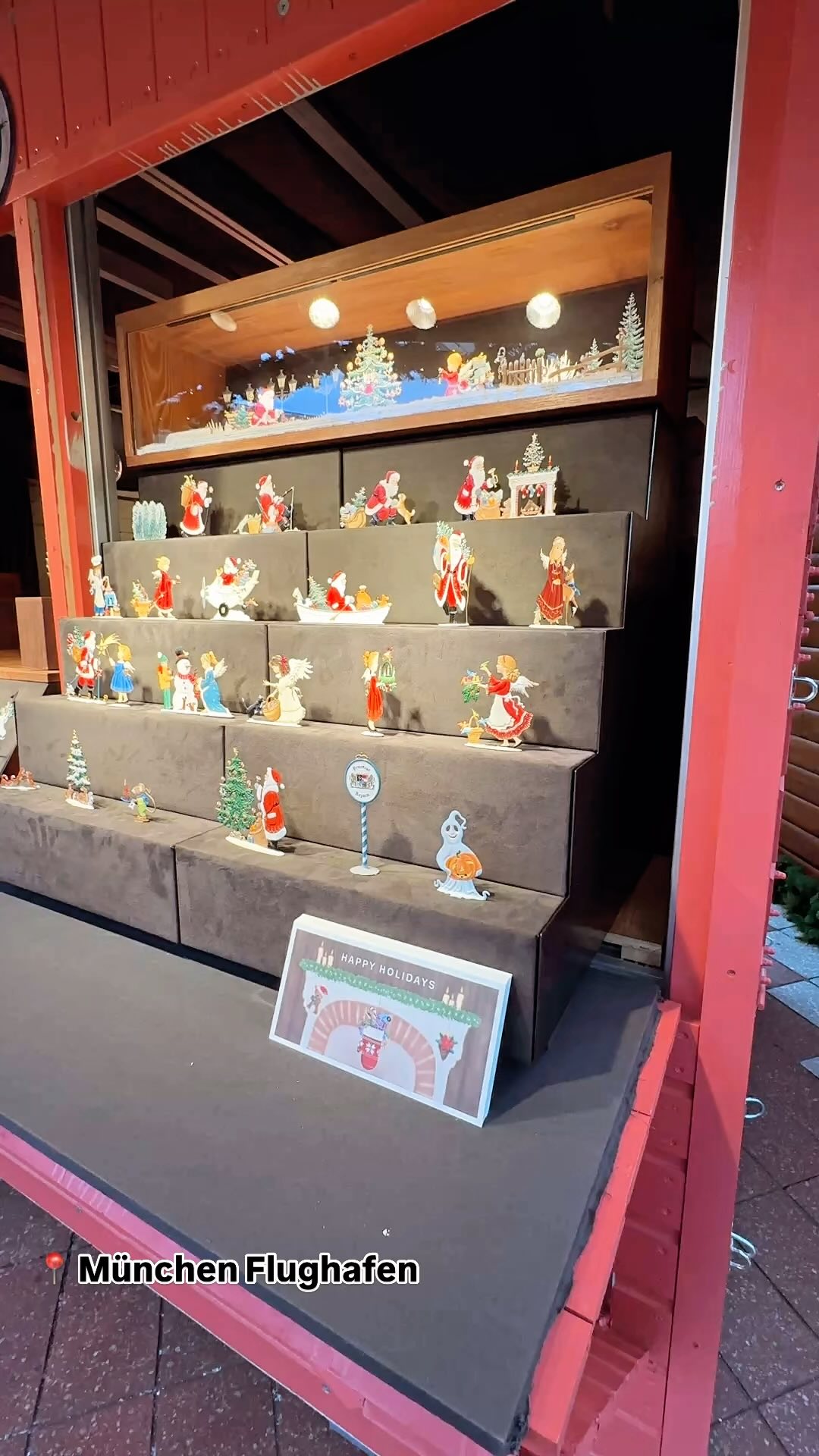
wilhelm.schweizer 🎄✨ Die Weihnachtszeit hat begonnen! Unser ikonischer Stand auf dem Weihnachtsmarkt am Münchner Flughafen ist geöffnet. Wir freuen uns, euch dort zu sehen! 🎁✈️ 🎄✨ The Christmas spirit has arrived! Our iconic booth at the Munich Airport Christmas Market is open and ready for you. We look forward to seeing you there! 🎁✈️ #WilhelmSchweizer #Zinnfiguren #WeihnachtsmarktMünchen #Weihnachtszauber #Handwerkskunst #Souvenir #GeschenkIdee #MunichChristmasMarket #ChristmasSpirit #Christmas #PewterFigurines #HolidayMagic
November 19 2024 • View on Instagram
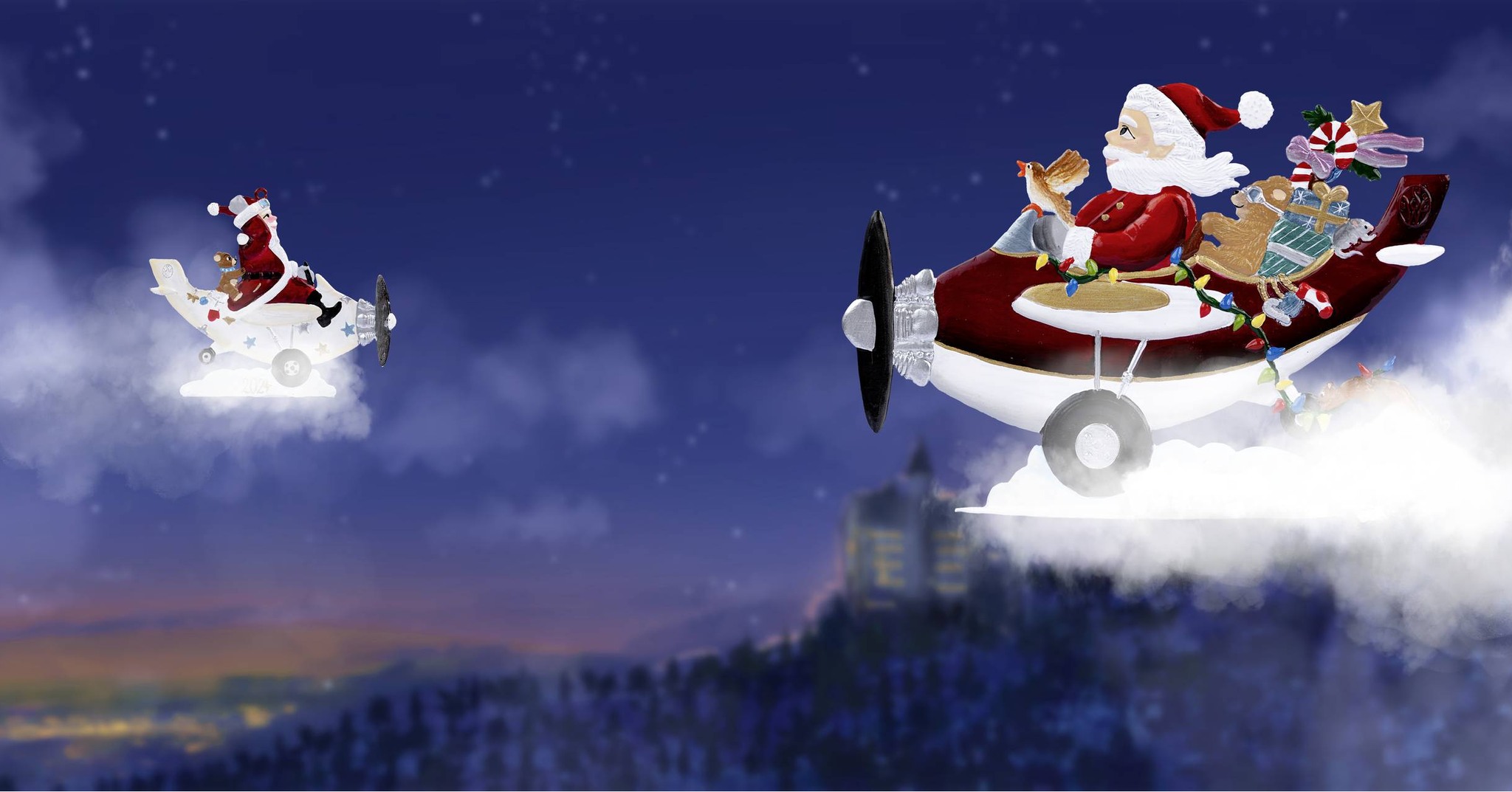
wilhelm.schweizer 🎅✨ GLOBALES GIVEAWAY! ✨🎅 Hey Zinn-Enthusiasten! Die festliche Jahreszeit ist da, und wir sind in großzügiger Stimmung! 🎁 Wir verlosen eine deiner Lieblings-Weihnachtsmannfiguren an einen glücklichen Gewinner - egal wo auf der Welt! Das perfekte Stück, um deinem Weihnachtsdekor etwas mehr Magie zu verleihen! ✨❤️ So kannst du teilnehmen: 1. Folge uns auf Instagram ✅ 2. Markiere 3 Freunde in den Kommentaren dieses Posts 👯♀️ 3. Fülle die Umfrage in unserem Profil-Link aus (als Dankeschön erhältst du einen 10 EUR Rabattcode für unseren Online-Shop! 💸) Beeil dich – die Teilnahme endet am 6. Dezember! Wir geben den glücklichen Gewinner am 8. Dezember bekannt und kontaktieren ihn. 🎉 Dieser handgefertigte Weihnachtsmann wurde mit viel Liebe und Sorgfalt für dich gemacht. Danke, dass du ein so wunderbarer Teil unserer Community bist – wir freuen uns darauf, die Weihnachtsfreude mit dir zu teilen! 🎄🎅 Viel Glück! 🍀✨ #Giveaway #Weihnachtsmann #Weihnachtsdeko #Handgefertigt #WilhelmSchweizer #Zinnfiguren #Weihnachten #Weihnachtsfreude #FestlicheStimmung #Rabatt #Gewinnspiel #Gewinne #Dekoration #ZinnEnthusiasten #GlobalGiveaway #ChristmasSpirit
November 15 2024 • View on Instagram
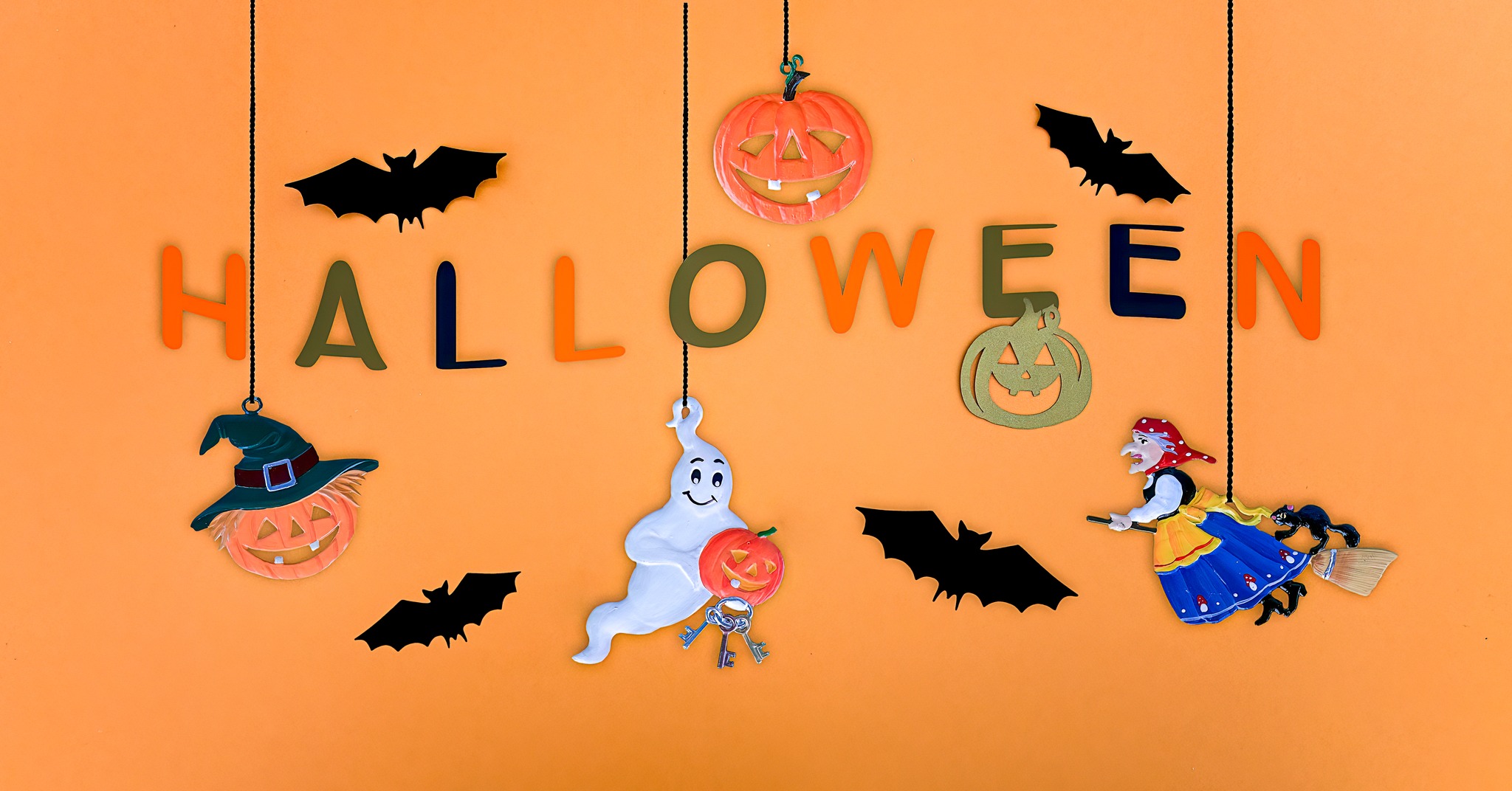
wilhelm.schweizer 🎃👻 Happy Halloween! 🎃👻Der Zauber der Saison mit unseren Figuren – perfekt für ein festlich-schauriges Zuhause! 🧙♀️✨ #HalloweenZauber #SpookySeason #Herbstgefühle #HalloweenDeko 🎃👻 Happy Halloween! 🎃👻 It’s the spookiest day of the year! Add a little magic to your home and celebrate with a playful Halloween vibe! 🧙♀️🦇 #HalloweenMagic #SpookySeason #FallFeels #TrickOrTreat #HalloweenDecor Artikel/ Items: Hexe Fliegt - 13201-BE Halloween Geist - 13213-BE Halloween-Kuerbis - 13211-BE Halloween Kuerbis Mit Hut - 13214-BE Weitere Informationen zu unserem Figurensortiment finden Sie unter www.zinnfiguren.de For further information on our figurine assortment please feel free to visit us at www.zinnfiguren.de #WilhelmSchweizer #HalloweenDecor #SpookyDecor #Handmade #GermanPewter #Handwerk #Kunstwerk #Ammersee #ShopOnline #WinterCollection #HangingOrnaments #UniqueGifts #EinzigartigeGeschenk #Halloween2024 #DekoInspiration #HalloweenDecor #FallDecor #Herbst2024
October 31 2024 • View on Instagram
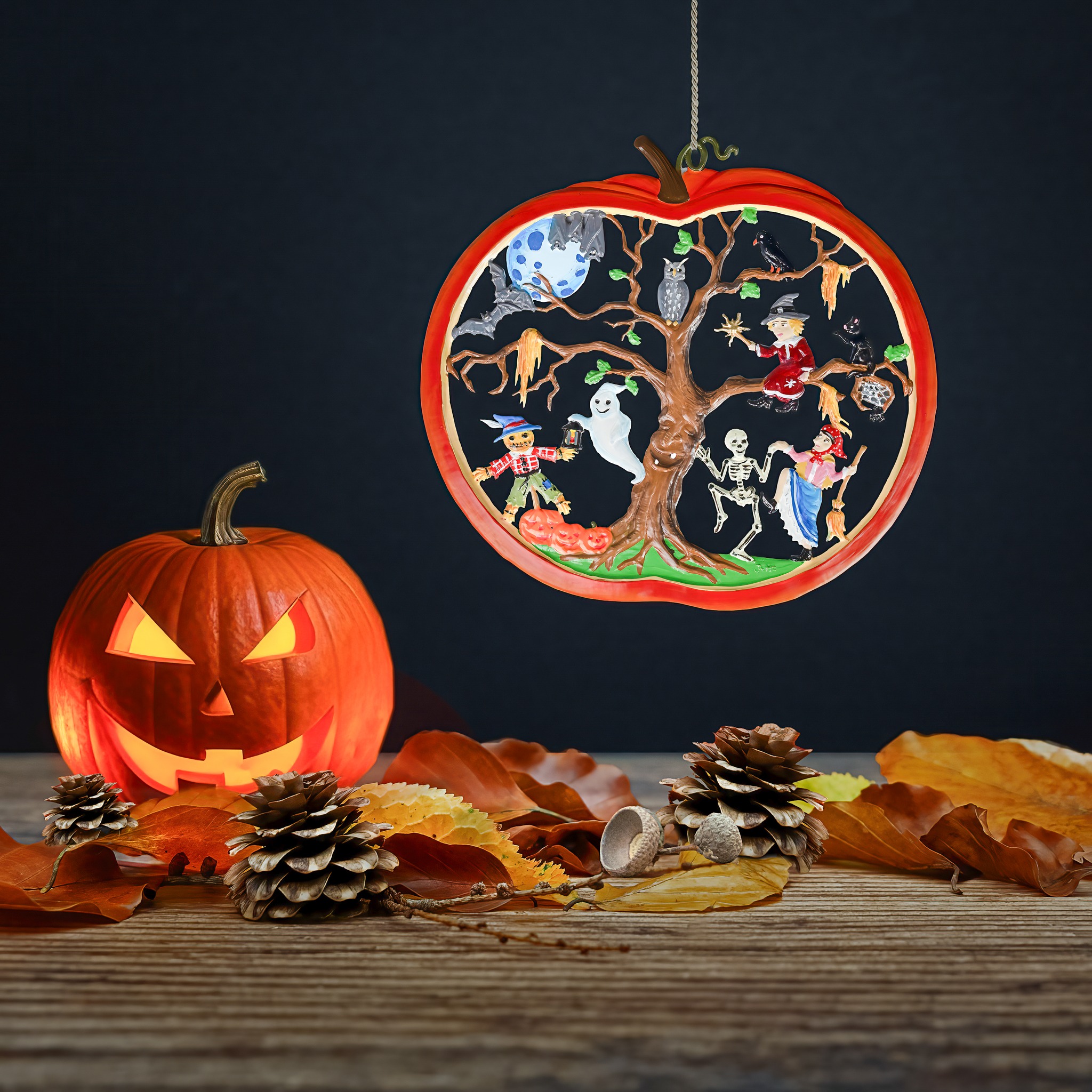
wilhelm.schweizer Tauchen Sie mit unserer bezaubernden Halloween-Kollektion in die gruselige Stimmung ein! 🎃👻 Hängen Sie diese festliche Szene auf, um Ihrer Halloween-Dekoration einen charmanten Zauber zu verleihen. #HalloweenMagie #GruselSaison #FestlicheDeko #WilhelmSchweizer Celebrate the spooky spirit with our enchanting Halloween collection! 🎃👻 Hang this festive scene to cast a charming spell over your Halloween decor. #HalloweenMagic #SpookySeason #FestiveDecor #wilhelmschweizer Artikel/ Items: Halloween - 9410HAL-BE Weitere Informationen zu unserem Figurensortiment finden Sie unter www.zinnfiguren.de For further information on our figurine assortment please feel free to visit us at www.zinnfiguren.de #Zinnfiguren #Halloween #HalloweenDecor #HerbstZeit #Handgemacht #EinzigartigeGeschenk #TrickOrTreat #ShopOnline #HomeDecor #WohnKultur #Kunstwerk #Ammersee #GermanPewter #Collectibles #AutumnVibes #GeschenkIdee #UniqueGifts
October 24 2024 • View on Instagram